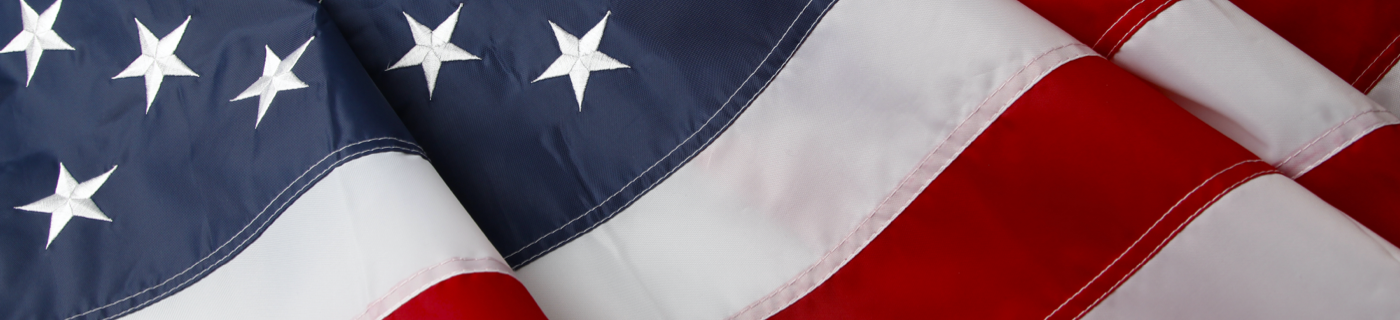
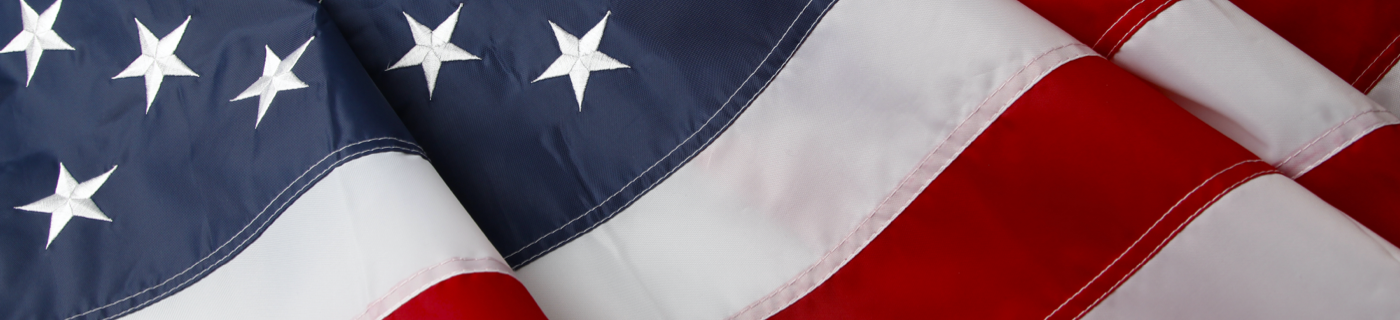
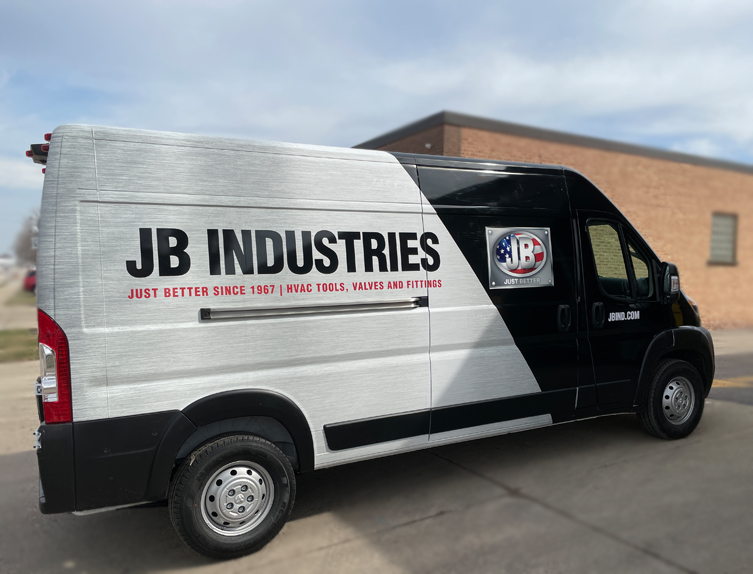
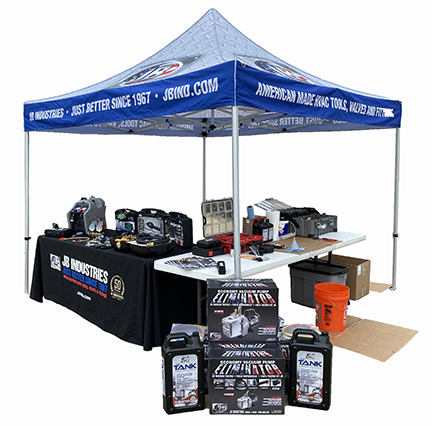
JB Industries believes in supporting every product we make that has the JB name on it. We have added a list of FAQs by category below to help you get the best performance out of your JB Product. If you can’t find the answer you’re needing please call Customer Service and they will be happy to help you. You can also check out JB Industries videos on YouTube. Customer Service 800.323.0811
Q&A
Why does my DS - 20000 Atlas scale shut off after a few minutes?
This scale has a battery saver feature that can be disabled and re-enabled.
Disabling the auto-shut off feature on the JB Atlas scale (DS-20000)
The Atlas scale is set to automatically shut off after 30 minutes if the weight reading does not change during that time. This feature can be disabled through the following procedure.
NOTE: Before attempting to disable auto-shut off, verify the software version of your scale, as the instructions are different for each version. Turn the scale on and observe the version that comes on the display;
Version 1.01 or 1.02
Turn scale off first, then hold the left and center buttons down, while pressing the power button down. The scale should read “JB Industries, ATLAS Ver. #. ##” then display a weight reading with “TEST MODE” below it.
Version 1.03 or higher
Turn the scale off first, then, hold the center button down while pressing the power button. The scale should read the same as the above description.
Press the middle button to scroll to the third option “AUTO OFF = YES”
Quickly press the zero button once: the display should now say ”AUTO OFF = NO”
Press and hold the zero button to save this setting and exit the test mode. You will see the words “TEST MODE” disappears. Once the scale exits test mode, only the weight reading will be displayed. The auto shut-off is now disabled.
If you wish to re-enable this feature, repeat the above procedure, and change the setting on the display “AUTO OFF= YES”
Why won’t my DS-20000S not link up to my phone?
Your scale has two buttons, the button on the left has an antenna symbol. If you press this until the yellow light stays on, it may link up then. If it doesn’t, you have two more attempts available. (4 channels/Bluetooth version)
I don't have a micron gauge so I leave the pump on the system for two to four hours, is this enough?
You can’t tell for sure. Without a micron gauge we do not know if the oil in the pump is clean. The oil in a vacuum pump acts as a blotter and absorbs all of the moisture and sediment in the system. As the oil becomes saturated, the efficiency of the pump is drastically reduced.
If I put new oil in now and run the pump the same period of time, am I safe?
Oil should be changed after every job and should only be changed when the oil is still hot. As the oil cools, the moisture separates from the oil and clings to the metal of the pump. Therefore, when changing the oil and not checking it with a micron gauge, you’re still guessing as to whether the pump can actually pull the proper vacuum to eliminate the moisture in the system.
I pull only from one side of the system using a micron gauge, but at times my gauge will jump up to a higher number. Is this right?
This can happen even if you pull on both sides of the system because there is a metering device to measure the pressure and refrigerant in the system. Air or moisture can be trapped in one side of the system and will eventually let go and therefore a higher reading on the micron gauge will occur. Sometimes moisture can be trapped in the oil of the compressor and when it escapes it will show up in the gauge.
I purchased a new micron gauge. How low of a vacuum should I pull?
Some manufacturers have a micron range that they want their system pulled down to, so therefore, JB can only suggest a micron reading. Our suggestion is to pull a system down to 250-300 microns only if you are also pulling a vacuum on the compressor. Going below 250 microns, you will start degassing the oil in the compressor and it will not be the same lubricating oil as it was originally. The oil will only degas and will not suck up into the vacuum pump.
It seems to take forever to pull down the system I am working on. Does this mean I have a leak or a lot of moisture in the unit?
Assuming that you are pulling on the high and low side of the system, did you remove the access valve cores? Leaving the cores in creates a big restriction and causes your vacuum to take a longer time to evacuate.
I bought a new micron gauge and I wanted to try it out with just my vacuum pump. I attached the gauge directly to the pump and it immediately went down. I then closed my blank off valve on my pump and the gauge went up very rapidly. Is the valve on my pump leaking?
No. The gauge is too close to the pump and it does not have a chance to equalize in pressure. To do this experiment correctly, connect your pump and a micron gauge to a small tank with only copper tubing or JB`s DV-29. Close the blank off valve as you did before and you will see a big difference in the reading.
You said with copper tubing, why not charging hoses?
Either copper tubing or metal hoses used in JB`s DV-29 are the only ways you can hold vacuum. Vacuum is critical for leaks, more so than refrigerant. Charging hoses, including environmental hoses, still permeate. Beyond permeation, where the hose ferrule is crimped to the hose, represents a potential leak under vacuum. Quick couplers with gaskets are not a good seal. When you screw down the male flare to the gasket quick coupler, the gasket goes into several contortions and will not seal properly. JB uses O-rings on our quick couplers and as you screw down the male flare you get a metal-to-metal seat and the O-ring lays around the flare to give it a perfect seal.
Then this means I cannot pull a vacuum on my system unless I use metal hose or copper tubing?
No. You can pull a vacuum with charging hoses, but when you want to blank off the system to check for leaks, you will need to use copper tubing or metal hoses.
I put my gauge connection to the pump when I am pulling a vacuum on a system, is this correct?
Many technicians do this for ease of hook-up, but remember with this set up you are actually reading what the pump is doing and not what the pump is doing to the system. To prove this theory, take a 50 foot coil of 1/4″ OD copper tubing, braze a flare on one end and a tee on the other. Attach a micron gauge to the male flare end, a gauge to the tee end, and a line from the tee to the pump. Turn the pump on and you will notice the side closest to the pump will be a lot lower than the other. Eventually, this will equalize out and give the same reading. This will occur in a system on which you are pulling a vacuum.
My (DV-22N/DV-41) vacuum gauge only reads zeroes across the screen when connected to a system.
First, test the gauge by connecting it to the pump, alone, without anything else, but the gauge connected to it and turn the pump on. Your gauge should read down into the two-digit rang within less than a minute. If that is ok, then the problem is in the system, or if the manifold and hose set are connected to the system. The newer DV-41 and DV-22N have a setting in the menu called ‘BARO-P’, which can help to get the gauge to read properly. DV-41- first make sure the gauge is not connected to any vacuum. Then hold the ‘mode’ button down until you hear it double-beep. ‘BARO-P’ will display first, then tap the mode button and ‘SET’ will display. Tap the mode button again, and you will see dashes across the screen, as in the warm up mode. Automatically, it will display ‘STORED’, and that calibration is complete. DV-22N- again, disconnect from any vacuum, then hold the right side arrow/enter button until a double-beep is heard. It will display ‘BARO-P’. Hold it down again until it reads ‘SET’. And once more for the dashes to display across the screen. It will automatically read ‘STORED’, and it’s ready. Sometimes, the problem is due to sensor being contaminated. Clean the sensor with (90-99% pure works best.) isopropyl alcohol. Do NOT use denatured alcohol. by squirting some into the sensor chamber using a dropper or a syringe, under the brass depressor. You can shake the unit sensor for a few seconds, then dump out the excess alcohol. Repeat this a few times. Or prop the unit or sensor upside down to prevent spillage, and let the alcohol soak inside overnight. Your vacuum pump will get rid of the alcohol left behind after dumping most of it out. You may have to remove the depressor beforehand, and replace the gasket as well.
My DMG2 gauge set is stuck at pressure reading (on one, or both sides.)
Hold down the ‘mode’ button and the other, to the right, with the play/stop symbols on it, simultaneously, for 10 seconds until the screen blanks out and release them both.
Within a few more seconds, the display will come back reading zero pressures on both sides.
I have a revolver manifold that leaks from one side into the manifold.
Apply some oil/lubricant to the “o” ring that keeps the hose holder in place.
Use a pair of screwdrivers to pop it off from the retainer fitting.
Use a 13/16” spark plug socket to unscrew the retainer fitting.
Do NOT use a 13/16” open end wrench.
You may need a hook tool to remove the white nylon gasket that holds the ball valve in place,
and throw it away. They are destroyed during removal.
Take a picture of the ball’s exact position before removal. This is easy to reverse on accident.
Tilt the manifold to remove the ball, push the stem inward to get it out of the way, then proceed to dig out the remaining gasket.
You will need;
(1- #3) MR-BVK ball valve kit
And possibly,
(1-#8) MR-504 ¼” hose holder kit
Remember to lube the stem and o rings before re-installing.
How do I get A JB planogram for my stores?
Contact your sales Rep to discuss JB products you carry and consistent space available in stores. Once a product list is determined the JB marketing team will put together a planogram and key with your JB products within 2-3 weeks.
How can I get JB merchandising displays?
You can place an order with Customer Service on the JB website under Distributor Marketing > Merchandising Displays or call Customer Service at 800.323.0811.
How can I get JB promotional merchandise?
Contact your Customer Service Representative. Available items can be viewed on the JB website under Distributor Marketing > Promotional Merchandise.
How can I get a JB logo for my marketing needs?
Located on the JB website under Distributor Marketing > Logos
How does the LD-5000 PROWLER sensor work?
As refrigerant gas enters the sensor, a tiny chemical reaction occurs that results in an electrical change inside the sensor element. This change (which is completely reversible and not depleting) is then detected by a microprocessor (computer chip) that translates the chemical reaction into an alarm signal.
Besides having superior sensitivity, especially to the newer HFC refrigerants, the Prowler sensor also operates at a lower temperature than heated sensors. This is an advantage because it draws less current and doesn't require the use of rechargeable batteries. Another advantage is that it can be used safely in combustible atmospheres.
Besides having superior sensitivity, especially to the newer HFC refrigerants, the Prowler sensor also operates at a lower temperature than heated sensors. This is an advantage because it draws less current and doesn’t require the use of rechargeable batteries. Another advantage is that it can be used safely in combustible atmospheres.
What happens when the LD-5000 PROWLER detects that a leak is present?
When refrigerant gas enters the sensor, the Prowler detection circuit initiates three indicators that show a leak is present. The user hears an audio alarm (when not manually muted), feels a vibration in the handle, and sees the bar graph line(s) appearing on the LCD screen. Both the audio and vibration alarm are constant no matter how large the concentration of the gas. The LCD bar graph changes depending on the concentration of the gas in the sensor. The bar graph is also independent from the sensitivity level selected.
How does the LD-5000 PROWLER work so that the source of the leak can be located?
Unlike other leak detectors, the Prowler incorporates several innovative high technology features that allow the user to find the source of the leak without requiring any manual adjustments. Advanced computer software constantly monitors the surroundings for the presence of refrigerant gas. The detector then automatically calibrates itself so that it alarms only when it senses an increase in the level of refrigerant as the source of the leak is approached. The proprietary software then “filters” out and virtually eliminates any unwanted (false) alarm signals that occur away from the leak source.
Will the LD-5000 PROWLER detect large leaks without any manual adjustments?
Yes. However, if the Prowler alarms initially close to a large leak and then stops alarming before the source of the leak can be pin pointed, it means that the concentration of refrigerant in the area near the leak is similar to the concentration at the leak source. In this situation, it is important to move the sensor away from the leak source (usually above the suspected leak source) for 5 to 10 seconds to allow the sensor to self-calibrate to a lower concentration before searching the area a second time. The detector will then alarm again closer to (or at) the source of the leak. Holding the probe away in this manner will also give a more accurate indication of the leak size on the bar graph.
Will the LD-5000 PROWLER alarm when entering a work area contaminated with refrigerant?
Yes. Nevertheless, you must always turn on the Prowler outside of the work area (in clean air) and allow it to complete the warm up cycle before entering an area where a large leak is suspected. The Prowler will alarm initially but will automatically self-calibrate to the surroundings and will not alarm again until a larger concentration closer to the source of the leak is detected.
Why does the alarm stop sounding when the sensor is held static at a leak source?
This is normal and demonstrates how the detector automatically resets (self-calibrates) itself to the ambient. Once the Prowler alarms near the area of the leak, it should be moved away from the leak and back again to verify the exact location and size of the leak. If the leak is large (more than five bars), it may be necessary to move the sensor away from the leak area for 5 to 10 seconds.
Can the LD-5000 PROWLER determine the size of the leak?
Yes, once the leak has been pin pointed the maximum number of bars on the LCD screen will give the user an idea of the size of the leak. If the leak is large, (5 bars or more) it may be necessary to hold the detector away from the leak for 5 to 10 seconds in order for the circuit to reset completely and to give an accurate indication of the leak size.
What does the LD-5000 PROWLER do when it is turned on and is going through the warm up mode?
When turned on, the Prowler begins to energize and condition the sensor for use. During this period, the unit will beep at a slow rate and the LCD bar graph will display the conditioning progress by gradually increasing. Warm up is complete when all 10 bars are shown on the display. The beep rate will also increase and the sensitivity level will default to Medium. NOTE: The bars on the bar graph may increase up initially and then down again before increasing to 10 full bars – this is normal.
How should the LD-5000 PROWLER be tested to make sure it is working properly prior to leak searching?
The preferred method to test the Prowler is with the Leak Test Vial that is included with the leak detector. Although the Vial does not contain refrigerant gas or liquid (this is prohibited), the media in the Vial accurately simulates a small to medium refrigerant gas leak. To test with the Vial, power on the Prowler by depressing the on/off button, allow the instrument time (up to 20 seconds) to energize the sensor, remove the plastic label seal on the top of the Leak Test Vial, and place the sensor closer to the small hole in the top of the Vile. The beep rate should increase and the Leak Size Bar Graph should display a minimum of three bars. The detector will calibrate itself to the Leak Test Vial if the sensor is held static close to the hole in the cap and will not alarm again until it is moved away and allowed to reset. Consecutive testing at the cap and moving away from Vial will eventually result in the detector calibrating itself to the Vial. In this case, the Prowler may require additional time away from the Vial in order to reset before it will alarm again at the Leak Vial. Never use the Leak Test Vial with the cap removed from the bottle. NOTE: If the detector has been out of use for weeks, it may be necessary to set the sensitivity level to HI initially when testing the Prowler with the Leak Test Vial.
Is there a way to test the LD-5000 PROWLER with Refrigerant Gas before leak checking:
If it is necessary to test the Prowler with refrigerant gas, a small leak can be simulated by removing a Schrader valve cap on an access port of an HVAC system and waiting a few minutes for the accumulated gas to escape. Cracking open and quickly closing the valve on a cylinder of refrigerant is another option; however, the area around the valve should be fanned to allow the gas to dissipate before testing with the Prowler. This test method is not advisable because it is difficult to control the amount of gas emitted from a refrigerant cylinder. Opening and closing the valve on a cylinder typically emits a large volume of refrigerant, which is not representative of an actual leak in an HVAC system. If the Prowler is tested this way, the procedure for finding large leaks (see above) should be followed. If the procedure for finding large leaks is not followed, the automatic calibration feature of the Prowler may cause it to appear to be insensitive.
Will the LD-5000 PROWLER sensor become damaged if it is exposed to a heavy stream of gas coming from the valve of a refrigerant cylinder?
No. However, exposing the sensor to a heavy stream of refrigerant will cause the sensor to “saturate” and it may take up to 15 or more seconds for the sensor to automatically calibrate and reset to its maximum sensitivity level. For this reason, using a refrigerant cylinder is not an advisable means to test the sensitivity of the Prowler to any particular refrigerant.
How can you claim the sensor will last up to 10 years?
The Prowler utilizes sensor technology that is based on room monitoring where sensors are required to be functioning continuously for years. Sensors used for this purpose cannot be depleted when contaminated with refrigerant or require any adjustment to operate at peak performance after running continuously for long periods. By converting continuous use into daily use, for a typical HVAC technician, it was determined using controlled test methods that the sensor would last more than 10 years (under ideal conditions). The sensor life test data was derived after testing the Prowler sensors continuously over a period of time.
My LD-5000 PROWLER false alarms when I bump or tap the wand.
The tip on the sensor will, after significant use, build up a layer of dust and other particles that will partially become dislodged from vibration and bumping. Some of these particles are small enough to activate the alarm as if it’s detecting a refrigerant leak. The tip is too small for cotton swabs, so roll up a small piece of tissue and run it thru, followed by a rinse with water. Replace the old filter and the difference in performance is immediate.
My LD-5000 Prowler is not warming up or detecting.
Take a close look at the outside of sensor itself. There is an alignment notch and groove on the side of it. If you can see any portion of the notch, the sensor is not plugged in all of the way, and just needs to be pushed in deeper until the notch is gone and the sensor will make contact with the socket. Check the very tip, on the sensor, to make sure it’s clear from a plug stopping it up. Sometimes nothing else works, because the socket was unscrewed from the gooseneck. If the socket was unscrewed, then the connecting wires inside are broken off, rendering the unit unrepairable in the field, and needs to be sent out for repair. These sockets are thread locked to the gooseneck during assembly, and are difficult to unscrew for good reason.
Some helpful pump day guidelines to increase participation, customer interaction and sales activity:
- Promote in advance
- Limit number of pumps per person to less than 5
- Request customer be present during servicing of pumps to allow for quality sales interaction time and to discuss new products
- Service vacuum pump, change oil, replace fittings, test, etc.
- Service micron gauges, clean transducer, replace o-ring as needed
- Service CLS hoses, rebuild fittings
- Train wholesaler and contractor on proper service techniques
- Train and promote new and existing JB products
- Use your sign in sheet to send out thank you and follow up emails
- Ask customers to take a photo with their serviced pump and post on social media with the tag #JBPumpDays
What does breaking a vacuum mean?
By breaking a vacuum you are relieving pressure from inside the pump. This can also prevent oil from going up your hoses. Always break the vacuum before shutting off your pump, you do this by either loosening your hoses or caps on the eliminator or opening the gas ballast on the platinum’s before shutting off your pump.
Why does my vacuum pump runs, but I cannot get a vacuum?
The coupler between the shaft of the pump and the shaft of the motor is either broken or slipping. Make sure the set screws are tight on the flats of the two shafts.
Why is it so important to change the oil often in my vacuum pump?
The proper oil in a vacuum pump acts as a blotter and absorbs all of the moisture and non-condensable. As the oil becomes saturated with these contaminants, the efficiency of the pump is dramatically reduced. Maintaining clean oil in the pump ensures that the pump will operate at peak efficiency and prolong its life.
Why is it important to change my oil when the pump is hot?
As the pump cools, the moisture and contaminates start to separate in the pump and when drained, the contaminants cling to the walls of the pump. When you refill the pump with new oil, those contaminants will mix in with the new oil as the pump warms up resulting in the new oil quickly becoming contaminated.
If I am always pulling a vacuum on clean, dry systems, is there a way to check my oil in the pump to see if it is contaminated and not have to change it so frequently?
It is recommended that a micron gauge be attached directly to the pump and should pull to 50 microns or lower if the oil is clean. If the micron gauge does not pull to 50 microns, it is an indication that the oil is becoming contaminated and should be changed.
Other than pulling air out of the system, how does my vacuum pump get rid of the moisture in the system?
Most two stage vacuum pumps will go low enough in vacuum and reduce the atmospheric pressure within the system, thus allowing boiling of the moisture at a lower temperature. Once the moisture is in a vapor form, it is readily removed by the pump.
Can I use any oil in my vacuum pump?
No. JB Black Gold oil is extremely pure and non-detergent. Black Gold is hydro processed which means it goes through a series of catalytic steps rendering the oil extremely refined, more viscous, and more stable. The result is a clear mineral oil that will alert you to contamination sooner as it becomes cloudy or milky.
What is a gas ballast and how do I use it?
On the initial pull of vacuum on a system, the gas ballast is open allowing the initial volume of air in the system to bypass the oil so as to not contaminate the oil immediately. When the pump starts to quiet down, close the gas ballast and the pump will start reducing atmospheric pressure in the system to boil the moisture and non-condensable.
What is a blank-off valve?
The blank-off valve acts no different than a water valve. Open it, and with the pump running you will get your desired vacuum. Close it, and with the pump running there is no vacuum.
If I use a larger CFM pump, will I be able to pull a vacuum on a system faster?
In most cases NO. Using a vacuum pump on air conditioning systems from 1 ton to 10 tons, you will not see the difference between a 3 CFM pump and a 10 CFM pump. For example, if you put a pump on a system and you notice within 2 minutes the pump quiets down and you cannot really feel any air leaving the exhaust. This means that there is no more CFM left in the system and you are now working with molecules. Thus, at this point if you replaced a 3 CFM pump with a 10 CFM pump, there is no change in vacuum or time.
What is a micron?
There are 25,400 microns in an inch. Therefore, with a compound gauge reading 0 inches to 30 inches, there are 762,000 microns.
Can I mount my micron gauge onto the vacuum pump?
It is not recommended to do so as you are reading what the pump is doing and not what the pump is doing to the system (see DV-29). It is suggested that you tee off on the suction side of the system and mount the gauge there.
I have been using my low side gauge to pull a vacuum, is this wrong?
YES. The low side gauge knows only atmospheric pressure and cannot sense moisture or non-condensable. A micron gauge is a heat sensing device that not only reads atmospheric pressure, but also measures the gases created by the vacuum pump as it boils the moisture. For example, if you were to pull a vacuum on an enclosed bottle of water, the low side gauge when pulling a vacuum will read a perfect vacuum. Using a micron gauge, it will immediately tell you with a high reading that you have a problem in your system.
I have been pulling a vacuum on my system using a micron gauge and cannot get it down to a low reading.
Another possibility is that some oil may have entered the micron gauge and is giving false readings. The remedy is to pour regular rubbing alcohol into the connector on the micron gauge, shake, and pour out (do not use a q-tip, rag, or any other material – use the liquid alcohol only). Do this about three times, then try to pull a vacuum with the gauge.
I am able to pull a vacuum on my system, but when I blank-off, the micron gauge rises rapidly.
Unless you are using JB`s DV-29, copper tubing, or flexible metal hoses, it is not recommended to use your existing manifold and hoses for blanking-off a system to check for leaks. Hoses work very well under high pressure. Vacuum is very critical in leaks, more so than pressure. All charging hoses, including the black hoses 1/4″ or 3/8″ permeate. Where the crimp is on the brass to the hose also has possible leak issues, and the gasket at the coupler is a major leak offender. The vacuum industry uses O-rings on most couplers. When you screw down on a gasket, it goes into many contortions and will not seal. When using an O-ring, you screw down on it to get a metal to metal seat and the O-ring lies around the lip of the flare giving it a positive seal.
Why does the micron gauge slowly fall back and then start to hold after pulling a vacuum and blanking-off?
The reason for this is there is equalization within the system. If you pull a vacuum lower, it will then fall back at a shorter range and hold.
Why do I need to check the oil level when the pump is running?
The reason for this is that if the vacuum is not broken before pumps are shut down the oil in the cover will seek the vacuum still in the cartridge and intake chamber. Then the oil level will drop in the sight glass and give the appearance of a low oil level. Then if the pump is refilled to the oil level line and the pump started, the oil that got sucked back into the cartridge and intake chamber will be kicked back into the cover and now you’ll be over filled and the oil will shoot out the handle (exhaust port).
ATLAS FAQs
Why does my DS - 20000 Atlas scale shut off after a few minutes?
This scale has a battery saver feature that can be disabled and re-enabled.
Disabling the auto-shut off feature on the JB Atlas scale (DS-20000)
The Atlas scale is set to automatically shut off after 30 minutes if the weight reading does not change during that time. This feature can be disabled through the following procedure.
NOTE: Before attempting to disable auto-shut off, verify the software version of your scale, as the instructions are different for each version. Turn the scale on and observe the version that comes on the display;
Version 1.01 or 1.02
Turn scale off first, then hold the left and center buttons down, while pressing the power button down. The scale should read “JB Industries, ATLAS Ver. #. ##” then display a weight reading with “TEST MODE” below it.
Version 1.03 or higher
Turn the scale off first, then, hold the center button down while pressing the power button. The scale should read the same as the above description.
Press the middle button to scroll to the third option “AUTO OFF = YES”
Quickly press the zero button once: the display should now say ”AUTO OFF = NO”
Press and hold the zero button to save this setting and exit the test mode. You will see the words “TEST MODE” disappears. Once the scale exits test mode, only the weight reading will be displayed. The auto shut-off is now disabled.
If you wish to re-enable this feature, repeat the above procedure, and change the setting on the display “AUTO OFF= YES”
Why won’t my DS-20000S not link up to my phone?
Your scale has two buttons, the button on the left has an antenna symbol. If you press this until the yellow light stays on, it may link up then. If it doesn’t, you have two more attempts available. (4 channels/Bluetooth version)
Digital Vacuum Micron Gauge FAQs
I don't have a micron gauge so I leave the pump on the system for two to four hours, is this enough?
You can’t tell for sure. Without a micron gauge we do not know if the oil in the pump is clean. The oil in a vacuum pump acts as a blotter and absorbs all of the moisture and sediment in the system. As the oil becomes saturated, the efficiency of the pump is drastically reduced.
If I put new oil in now and run the pump the same period of time, am I safe?
Oil should be changed after every job and should only be changed when the oil is still hot. As the oil cools, the moisture separates from the oil and clings to the metal of the pump. Therefore, when changing the oil and not checking it with a micron gauge, you’re still guessing as to whether the pump can actually pull the proper vacuum to eliminate the moisture in the system.
I pull only from one side of the system using a micron gauge, but at times my gauge will jump up to a higher number. Is this right?
This can happen even if you pull on both sides of the system because there is a metering device to measure the pressure and refrigerant in the system. Air or moisture can be trapped in one side of the system and will eventually let go and therefore a higher reading on the micron gauge will occur. Sometimes moisture can be trapped in the oil of the compressor and when it escapes it will show up in the gauge.
I purchased a new micron gauge. How low of a vacuum should I pull?
Some manufacturers have a micron range that they want their system pulled down to, so therefore, JB can only suggest a micron reading. Our suggestion is to pull a system down to 250-300 microns only if you are also pulling a vacuum on the compressor. Going below 250 microns, you will start degassing the oil in the compressor and it will not be the same lubricating oil as it was originally. The oil will only degas and will not suck up into the vacuum pump.
It seems to take forever to pull down the system I am working on. Does this mean I have a leak or a lot of moisture in the unit?
Assuming that you are pulling on the high and low side of the system, did you remove the access valve cores? Leaving the cores in creates a big restriction and causes your vacuum to take a longer time to evacuate.
I bought a new micron gauge and I wanted to try it out with just my vacuum pump. I attached the gauge directly to the pump and it immediately went down. I then closed my blank off valve on my pump and the gauge went up very rapidly. Is the valve on my pump leaking?
No. The gauge is too close to the pump and it does not have a chance to equalize in pressure. To do this experiment correctly, connect your pump and a micron gauge to a small tank with only copper tubing or JB`s DV-29. Close the blank off valve as you did before and you will see a big difference in the reading.
You said with copper tubing, why not charging hoses?
Either copper tubing or metal hoses used in JB`s DV-29 are the only ways you can hold vacuum. Vacuum is critical for leaks, more so than refrigerant. Charging hoses, including environmental hoses, still permeate. Beyond permeation, where the hose ferrule is crimped to the hose, represents a potential leak under vacuum. Quick couplers with gaskets are not a good seal. When you screw down the male flare to the gasket quick coupler, the gasket goes into several contortions and will not seal properly. JB uses O-rings on our quick couplers and as you screw down the male flare you get a metal-to-metal seat and the O-ring lays around the flare to give it a perfect seal.
Then this means I cannot pull a vacuum on my system unless I use metal hose or copper tubing?
No. You can pull a vacuum with charging hoses, but when you want to blank off the system to check for leaks, you will need to use copper tubing or metal hoses.
I put my gauge connection to the pump when I am pulling a vacuum on a system, is this correct?
Many technicians do this for ease of hook-up, but remember with this set up you are actually reading what the pump is doing and not what the pump is doing to the system. To prove this theory, take a 50 foot coil of 1/4″ OD copper tubing, braze a flare on one end and a tee on the other. Attach a micron gauge to the male flare end, a gauge to the tee end, and a line from the tee to the pump. Turn the pump on and you will notice the side closest to the pump will be a lot lower than the other. Eventually, this will equalize out and give the same reading. This will occur in a system on which you are pulling a vacuum.
My (DV-22N/DV-41) vacuum gauge only reads zeroes across the screen when connected to a system.
First, test the gauge by connecting it to the pump, alone, without anything else, but the gauge connected to it and turn the pump on. Your gauge should read down into the two-digit rang within less than a minute. If that is ok, then the problem is in the system, or if the manifold and hose set are connected to the system. The newer DV-41 and DV-22N have a setting in the menu called ‘BARO-P’, which can help to get the gauge to read properly. DV-41- first make sure the gauge is not connected to any vacuum. Then hold the ‘mode’ button down until you hear it double-beep. ‘BARO-P’ will display first, then tap the mode button and ‘SET’ will display. Tap the mode button again, and you will see dashes across the screen, as in the warm up mode. Automatically, it will display ‘STORED’, and that calibration is complete. DV-22N- again, disconnect from any vacuum, then hold the right side arrow/enter button until a double-beep is heard. It will display ‘BARO-P’. Hold it down again until it reads ‘SET’. And once more for the dashes to display across the screen. It will automatically read ‘STORED’, and it’s ready. Sometimes, the problem is due to sensor being contaminated. Clean the sensor with (90-99% pure works best.) isopropyl alcohol. Do NOT use denatured alcohol. by squirting some into the sensor chamber using a dropper or a syringe, under the brass depressor. You can shake the unit sensor for a few seconds, then dump out the excess alcohol. Repeat this a few times. Or prop the unit or sensor upside down to prevent spillage, and let the alcohol soak inside overnight. Your vacuum pump will get rid of the alcohol left behind after dumping most of it out. You may have to remove the depressor beforehand, and replace the gasket as well.
Manifold FAQs
My DMG2 gauge set is stuck at pressure reading (on one, or both sides.)
Hold down the ‘mode’ button and the other, to the right, with the play/stop symbols on it, simultaneously, for 10 seconds until the screen blanks out and release them both.
Within a few more seconds, the display will come back reading zero pressures on both sides.
I have a revolver manifold that leaks from one side into the manifold.
Apply some oil/lubricant to the “o” ring that keeps the hose holder in place.
Use a pair of screwdrivers to pop it off from the retainer fitting.
Use a 13/16” spark plug socket to unscrew the retainer fitting.
Do NOT use a 13/16” open end wrench.
You may need a hook tool to remove the white nylon gasket that holds the ball valve in place,
and throw it away. They are destroyed during removal.
Take a picture of the ball’s exact position before removal. This is easy to reverse on accident.
Tilt the manifold to remove the ball, push the stem inward to get it out of the way, then proceed to dig out the remaining gasket.
You will need;
(1- #3) MR-BVK ball valve kit
And possibly,
(1-#8) MR-504 ¼” hose holder kit
Remember to lube the stem and o rings before re-installing.
Marketing FAQs
How do I get A JB planogram for my stores?
Contact your sales Rep to discuss JB products you carry and consistent space available in stores. Once a product list is determined the JB marketing team will put together a planogram and key with your JB products within 2-3 weeks.
How can I get JB merchandising displays?
You can place an order with Customer Service on the JB website under Distributor Marketing > Merchandising Displays or call Customer Service at 800.323.0811.
How can I get JB promotional merchandise?
Contact your Customer Service Representative. Available items can be viewed on the JB website under Distributor Marketing > Promotional Merchandise.
How can I get a JB logo for my marketing needs?
Located on the JB website under Distributor Marketing > Logos
Prowler LD-5000 FAQs
How does the LD-5000 PROWLER sensor work?
As refrigerant gas enters the sensor, a tiny chemical reaction occurs that results in an electrical change inside the sensor element. This change (which is completely reversible and not depleting) is then detected by a microprocessor (computer chip) that translates the chemical reaction into an alarm signal.
Besides having superior sensitivity, especially to the newer HFC refrigerants, the Prowler sensor also operates at a lower temperature than heated sensors. This is an advantage because it draws less current and doesn't require the use of rechargeable batteries. Another advantage is that it can be used safely in combustible atmospheres.
Besides having superior sensitivity, especially to the newer HFC refrigerants, the Prowler sensor also operates at a lower temperature than heated sensors. This is an advantage because it draws less current and doesn’t require the use of rechargeable batteries. Another advantage is that it can be used safely in combustible atmospheres.
What happens when the LD-5000 PROWLER detects that a leak is present?
When refrigerant gas enters the sensor, the Prowler detection circuit initiates three indicators that show a leak is present. The user hears an audio alarm (when not manually muted), feels a vibration in the handle, and sees the bar graph line(s) appearing on the LCD screen. Both the audio and vibration alarm are constant no matter how large the concentration of the gas. The LCD bar graph changes depending on the concentration of the gas in the sensor. The bar graph is also independent from the sensitivity level selected.
How does the LD-5000 PROWLER work so that the source of the leak can be located?
Unlike other leak detectors, the Prowler incorporates several innovative high technology features that allow the user to find the source of the leak without requiring any manual adjustments. Advanced computer software constantly monitors the surroundings for the presence of refrigerant gas. The detector then automatically calibrates itself so that it alarms only when it senses an increase in the level of refrigerant as the source of the leak is approached. The proprietary software then “filters” out and virtually eliminates any unwanted (false) alarm signals that occur away from the leak source.
Will the LD-5000 PROWLER detect large leaks without any manual adjustments?
Yes. However, if the Prowler alarms initially close to a large leak and then stops alarming before the source of the leak can be pin pointed, it means that the concentration of refrigerant in the area near the leak is similar to the concentration at the leak source. In this situation, it is important to move the sensor away from the leak source (usually above the suspected leak source) for 5 to 10 seconds to allow the sensor to self-calibrate to a lower concentration before searching the area a second time. The detector will then alarm again closer to (or at) the source of the leak. Holding the probe away in this manner will also give a more accurate indication of the leak size on the bar graph.
Will the LD-5000 PROWLER alarm when entering a work area contaminated with refrigerant?
Yes. Nevertheless, you must always turn on the Prowler outside of the work area (in clean air) and allow it to complete the warm up cycle before entering an area where a large leak is suspected. The Prowler will alarm initially but will automatically self-calibrate to the surroundings and will not alarm again until a larger concentration closer to the source of the leak is detected.
Why does the alarm stop sounding when the sensor is held static at a leak source?
This is normal and demonstrates how the detector automatically resets (self-calibrates) itself to the ambient. Once the Prowler alarms near the area of the leak, it should be moved away from the leak and back again to verify the exact location and size of the leak. If the leak is large (more than five bars), it may be necessary to move the sensor away from the leak area for 5 to 10 seconds.
Can the LD-5000 PROWLER determine the size of the leak?
Yes, once the leak has been pin pointed the maximum number of bars on the LCD screen will give the user an idea of the size of the leak. If the leak is large, (5 bars or more) it may be necessary to hold the detector away from the leak for 5 to 10 seconds in order for the circuit to reset completely and to give an accurate indication of the leak size.
What does the LD-5000 PROWLER do when it is turned on and is going through the warm up mode?
When turned on, the Prowler begins to energize and condition the sensor for use. During this period, the unit will beep at a slow rate and the LCD bar graph will display the conditioning progress by gradually increasing. Warm up is complete when all 10 bars are shown on the display. The beep rate will also increase and the sensitivity level will default to Medium. NOTE: The bars on the bar graph may increase up initially and then down again before increasing to 10 full bars – this is normal.
How should the LD-5000 PROWLER be tested to make sure it is working properly prior to leak searching?
The preferred method to test the Prowler is with the Leak Test Vial that is included with the leak detector. Although the Vial does not contain refrigerant gas or liquid (this is prohibited), the media in the Vial accurately simulates a small to medium refrigerant gas leak. To test with the Vial, power on the Prowler by depressing the on/off button, allow the instrument time (up to 20 seconds) to energize the sensor, remove the plastic label seal on the top of the Leak Test Vial, and place the sensor closer to the small hole in the top of the Vile. The beep rate should increase and the Leak Size Bar Graph should display a minimum of three bars. The detector will calibrate itself to the Leak Test Vial if the sensor is held static close to the hole in the cap and will not alarm again until it is moved away and allowed to reset. Consecutive testing at the cap and moving away from Vial will eventually result in the detector calibrating itself to the Vial. In this case, the Prowler may require additional time away from the Vial in order to reset before it will alarm again at the Leak Vial. Never use the Leak Test Vial with the cap removed from the bottle. NOTE: If the detector has been out of use for weeks, it may be necessary to set the sensitivity level to HI initially when testing the Prowler with the Leak Test Vial.
Is there a way to test the LD-5000 PROWLER with Refrigerant Gas before leak checking:
If it is necessary to test the Prowler with refrigerant gas, a small leak can be simulated by removing a Schrader valve cap on an access port of an HVAC system and waiting a few minutes for the accumulated gas to escape. Cracking open and quickly closing the valve on a cylinder of refrigerant is another option; however, the area around the valve should be fanned to allow the gas to dissipate before testing with the Prowler. This test method is not advisable because it is difficult to control the amount of gas emitted from a refrigerant cylinder. Opening and closing the valve on a cylinder typically emits a large volume of refrigerant, which is not representative of an actual leak in an HVAC system. If the Prowler is tested this way, the procedure for finding large leaks (see above) should be followed. If the procedure for finding large leaks is not followed, the automatic calibration feature of the Prowler may cause it to appear to be insensitive.
Will the LD-5000 PROWLER sensor become damaged if it is exposed to a heavy stream of gas coming from the valve of a refrigerant cylinder?
No. However, exposing the sensor to a heavy stream of refrigerant will cause the sensor to “saturate” and it may take up to 15 or more seconds for the sensor to automatically calibrate and reset to its maximum sensitivity level. For this reason, using a refrigerant cylinder is not an advisable means to test the sensitivity of the Prowler to any particular refrigerant.
How can you claim the sensor will last up to 10 years?
The Prowler utilizes sensor technology that is based on room monitoring where sensors are required to be functioning continuously for years. Sensors used for this purpose cannot be depleted when contaminated with refrigerant or require any adjustment to operate at peak performance after running continuously for long periods. By converting continuous use into daily use, for a typical HVAC technician, it was determined using controlled test methods that the sensor would last more than 10 years (under ideal conditions). The sensor life test data was derived after testing the Prowler sensors continuously over a period of time.
My LD-5000 PROWLER false alarms when I bump or tap the wand.
The tip on the sensor will, after significant use, build up a layer of dust and other particles that will partially become dislodged from vibration and bumping. Some of these particles are small enough to activate the alarm as if it’s detecting a refrigerant leak. The tip is too small for cotton swabs, so roll up a small piece of tissue and run it thru, followed by a rinse with water. Replace the old filter and the difference in performance is immediate.
My LD-5000 Prowler is not warming up or detecting.
Take a close look at the outside of sensor itself. There is an alignment notch and groove on the side of it. If you can see any portion of the notch, the sensor is not plugged in all of the way, and just needs to be pushed in deeper until the notch is gone and the sensor will make contact with the socket. Check the very tip, on the sensor, to make sure it’s clear from a plug stopping it up. Sometimes nothing else works, because the socket was unscrewed from the gooseneck. If the socket was unscrewed, then the connecting wires inside are broken off, rendering the unit unrepairable in the field, and needs to be sent out for repair. These sockets are thread locked to the gooseneck during assembly, and are difficult to unscrew for good reason.
Pump Day FAQs
Some helpful pump day guidelines to increase participation, customer interaction and sales activity:
- Promote in advance
- Limit number of pumps per person to less than 5
- Request customer be present during servicing of pumps to allow for quality sales interaction time and to discuss new products
- Service vacuum pump, change oil, replace fittings, test, etc.
- Service micron gauges, clean transducer, replace o-ring as needed
- Service CLS hoses, rebuild fittings
- Train wholesaler and contractor on proper service techniques
- Train and promote new and existing JB products
- Use your sign in sheet to send out thank you and follow up emails
- Ask customers to take a photo with their serviced pump and post on social media with the tag #JBPumpDays
Vacuum Pump FAQs
What does breaking a vacuum mean?
By breaking a vacuum you are relieving pressure from inside the pump. This can also prevent oil from going up your hoses. Always break the vacuum before shutting off your pump, you do this by either loosening your hoses or caps on the eliminator or opening the gas ballast on the platinum’s before shutting off your pump.
Why does my vacuum pump runs, but I cannot get a vacuum?
The coupler between the shaft of the pump and the shaft of the motor is either broken or slipping. Make sure the set screws are tight on the flats of the two shafts.
Why is it so important to change the oil often in my vacuum pump?
The proper oil in a vacuum pump acts as a blotter and absorbs all of the moisture and non-condensable. As the oil becomes saturated with these contaminants, the efficiency of the pump is dramatically reduced. Maintaining clean oil in the pump ensures that the pump will operate at peak efficiency and prolong its life.
Why is it important to change my oil when the pump is hot?
As the pump cools, the moisture and contaminates start to separate in the pump and when drained, the contaminants cling to the walls of the pump. When you refill the pump with new oil, those contaminants will mix in with the new oil as the pump warms up resulting in the new oil quickly becoming contaminated.
If I am always pulling a vacuum on clean, dry systems, is there a way to check my oil in the pump to see if it is contaminated and not have to change it so frequently?
It is recommended that a micron gauge be attached directly to the pump and should pull to 50 microns or lower if the oil is clean. If the micron gauge does not pull to 50 microns, it is an indication that the oil is becoming contaminated and should be changed.
Other than pulling air out of the system, how does my vacuum pump get rid of the moisture in the system?
Most two stage vacuum pumps will go low enough in vacuum and reduce the atmospheric pressure within the system, thus allowing boiling of the moisture at a lower temperature. Once the moisture is in a vapor form, it is readily removed by the pump.
Can I use any oil in my vacuum pump?
No. JB Black Gold oil is extremely pure and non-detergent. Black Gold is hydro processed which means it goes through a series of catalytic steps rendering the oil extremely refined, more viscous, and more stable. The result is a clear mineral oil that will alert you to contamination sooner as it becomes cloudy or milky.
What is a gas ballast and how do I use it?
On the initial pull of vacuum on a system, the gas ballast is open allowing the initial volume of air in the system to bypass the oil so as to not contaminate the oil immediately. When the pump starts to quiet down, close the gas ballast and the pump will start reducing atmospheric pressure in the system to boil the moisture and non-condensable.
What is a blank-off valve?
The blank-off valve acts no different than a water valve. Open it, and with the pump running you will get your desired vacuum. Close it, and with the pump running there is no vacuum.
If I use a larger CFM pump, will I be able to pull a vacuum on a system faster?
In most cases NO. Using a vacuum pump on air conditioning systems from 1 ton to 10 tons, you will not see the difference between a 3 CFM pump and a 10 CFM pump. For example, if you put a pump on a system and you notice within 2 minutes the pump quiets down and you cannot really feel any air leaving the exhaust. This means that there is no more CFM left in the system and you are now working with molecules. Thus, at this point if you replaced a 3 CFM pump with a 10 CFM pump, there is no change in vacuum or time.
What is a micron?
There are 25,400 microns in an inch. Therefore, with a compound gauge reading 0 inches to 30 inches, there are 762,000 microns.
Can I mount my micron gauge onto the vacuum pump?
It is not recommended to do so as you are reading what the pump is doing and not what the pump is doing to the system (see DV-29). It is suggested that you tee off on the suction side of the system and mount the gauge there.
I have been using my low side gauge to pull a vacuum, is this wrong?
YES. The low side gauge knows only atmospheric pressure and cannot sense moisture or non-condensable. A micron gauge is a heat sensing device that not only reads atmospheric pressure, but also measures the gases created by the vacuum pump as it boils the moisture. For example, if you were to pull a vacuum on an enclosed bottle of water, the low side gauge when pulling a vacuum will read a perfect vacuum. Using a micron gauge, it will immediately tell you with a high reading that you have a problem in your system.
I have been pulling a vacuum on my system using a micron gauge and cannot get it down to a low reading.
Another possibility is that some oil may have entered the micron gauge and is giving false readings. The remedy is to pour regular rubbing alcohol into the connector on the micron gauge, shake, and pour out (do not use a q-tip, rag, or any other material – use the liquid alcohol only). Do this about three times, then try to pull a vacuum with the gauge.
I am able to pull a vacuum on my system, but when I blank-off, the micron gauge rises rapidly.
Unless you are using JB`s DV-29, copper tubing, or flexible metal hoses, it is not recommended to use your existing manifold and hoses for blanking-off a system to check for leaks. Hoses work very well under high pressure. Vacuum is very critical in leaks, more so than pressure. All charging hoses, including the black hoses 1/4″ or 3/8″ permeate. Where the crimp is on the brass to the hose also has possible leak issues, and the gasket at the coupler is a major leak offender. The vacuum industry uses O-rings on most couplers. When you screw down on a gasket, it goes into many contortions and will not seal. When using an O-ring, you screw down on it to get a metal to metal seat and the O-ring lies around the lip of the flare giving it a positive seal.
Why does the micron gauge slowly fall back and then start to hold after pulling a vacuum and blanking-off?
The reason for this is there is equalization within the system. If you pull a vacuum lower, it will then fall back at a shorter range and hold.
Why do I need to check the oil level when the pump is running?
The reason for this is that if the vacuum is not broken before pumps are shut down the oil in the cover will seek the vacuum still in the cartridge and intake chamber. Then the oil level will drop in the sight glass and give the appearance of a low oil level. Then if the pump is refilled to the oil level line and the pump started, the oil that got sucked back into the cartridge and intake chamber will be kicked back into the cover and now you’ll be over filled and the oil will shoot out the handle (exhaust port).